DESCUBRE NUESTRO CANAL DE YOUTUBE
¿Cómo se transporta y cómo funciona un regasificador de gas natural líquido?
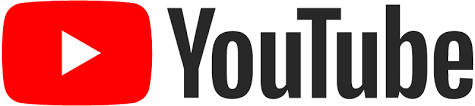
¿Cómo se transporta y cómo funciona un regasificador de gas natural líquido?
En nuestro vídeo anterior hablamos del gas natural y sus características, viendo en detalle todos los pasos necesarios para su extracción y los tipos de instalaciones.
Como ya hemos dicho, el gas extraído se refina y se transporta, a través de gasoductos o metanoductos, a instalaciones eléctricas y hogares.
Pero, ¿cómo se transporta el gas extraído del yacimiento a su usuario final? En el mejor de los casos, se transporta por tierra con metanoductos, a territorios que tienen la suerte de estar conectados a países proveedores, como la mayoría de los países europeos con Rusia. Para los países que no tienen estas posibilidades, deben comprar el producto a los países que transportan gas natural por mar.
El transporte marítimo del gas natural es muy delicado, hablamos de un producto compuesto por un 98% de metano, altamente inflamable, y transportarlo en grandes tanques instalados en un barco puede ser particularmente riesgoso.
Es por eso que hay que llevar el gas natural de su estado aeriforme a su estado líquido. El gas natural líquido, también llamado GNL (LNG en inglés), no es inflamable como en el estado aeriforme, además el volumen del gas se reduce 600 veces, facilitando y aumentando la capacidad de transporte de los buques metaneros en un solo viaje. Los buques metaneros son embarcaciones especiales construidas especialmente para el transporte de metano y gases inflamables.
Ahora veamos en detalle la cadena de suministro y tratamiento del gas natural.
Después de la extracción del producto, con la ayuda de metanoductos, el gas se transporta a instalaciones especiales que procederán a su licuefacción; las instalaciones pueden encontrarse cerca de las costas, normalmente en zonas portuarias, o en instalaciones off-shore, con estructuras flotantes ancladas al fondo marino.
Para llevar el gas al estado líquido, se inicia con un tratamiento de eliminación del dióxido de carbono y del sulfuro de hidrógeno, a continuación se realiza un preenfriamiento y se procede con la extracción de eventuales componentes pesados. En este punto, la temperatura del gas se reduce drásticamente a -163°C, por debajo de la temperatura de ebullición del metano, principal componente del gas natural.
Con tubos criogénicos, ubicados en muelles de carga, se inyecta gas natural licuado dentro de los tanques colocados en los buques metaneros. Estos barcos pueden transportar entre 150 y 200 mil metros cúbicos de metano, y existen dos tipos:
- El primer ejemplo es el de un barco con tanques integrados desarrollado por Gaztransport & Technigaz. Para esta tipología existen 2 versiones: la de Technigaz con depósitos constituidos por una barrera primaria elástica, formada por una membrana con nervaduras realizada con placas de acero; la disposición de las placas forma dos órdenes de nervaduras ortogonales entre sí y tienen la función de reducir las tensiones térmicas. La barrera secundaria está realizada con un material compuesto, el “tríplex”, consistente en una lámina de aluminio en un wafer de tejido de fibra de vidrio. El depósito se fija al casco interior con una espuma de poliuretano reforzada con fibras de vidrio. En cambio, la tipología desarrollada por Gaztransport prevé dos barreras compuestas por planchas planas soldadas (???), realizadas en una particular aleación metálica de acero y níquel, denominada “Invar”. Entre las dos barreras hay paneles aislantes y cámaras de aire, en las que se inyecta nitrógeno líquido para mantener la temperatura criogénica del gas natural. En este caso, el tanque se mantiene en el casco interno con cajas de aislamiento térmico de madera de balsa llenas de perlita.
- Otro ejemplo de buque metanero con tanques autoportante: la empresa Moss Rosenberg se enfrentó al problema de la resistencia a los esfuerzos inducidos por el peso del gas natural en los tanques, para solucionarlo diseñó buques metaneros con 4 o 6 tanques esféricos. Las bolas están aisladas con una capa de material aislante, entre ellas se pasa una cámara llena de nitrógeno para aumentar la capacidad de aislamiento y mantener baja la temperatura del tanque. Cada esfera está sostenida por una camisa cilíndrica que descansa sobre el casco del barco; este último está protegido de posibles fugas de gas con una barrera secundaria colocada en la base de las esferas.
El transportador de GNL transporta su carga de GNL a la planta de regasificación; tras haber sido fondeados y haber realizado la conexión a los brazos de descarga de las instalaciones portuarias, comienzan a trasvasar el GNL a los tanques de almacenamiento. Las plantas de regasificación pueden estar ubicadas en zonas portuarias, por lo que hablamos de una planta onshore en tierra firme, o de una plataforma, apoyada en el fondo del mar, que toma el nombre de offshore gravity based, o de floating storage and regasification unit, FSRU, un buque metanero, convertido para regasificación, anclado al fondo del mar, pero este tipo lo veremos más adelante.
Como ya hemos dicho, el gas extraído se refina y se transporta, a través de gasoductos o metanoductos, a instalaciones eléctricas y hogares.
Pero, ¿cómo se transporta el gas extraído del yacimiento a su usuario final? En el mejor de los casos, se transporta por tierra con metanoductos, a territorios que tienen la suerte de estar conectados a países proveedores, como la mayoría de los países europeos con Rusia. Para los países que no tienen estas posibilidades, deben comprar el producto a los países que transportan gas natural por mar.
El transporte marítimo del gas natural es muy delicado, hablamos de un producto compuesto por un 98% de metano, altamente inflamable, y transportarlo en grandes tanques instalados en un barco puede ser particularmente riesgoso.
Es por eso que hay que llevar el gas natural de su estado aeriforme a su estado líquido. El gas natural líquido, también llamado GNL (LNG en inglés), no es inflamable como en el estado aeriforme, además el volumen del gas se reduce 600 veces, facilitando y aumentando la capacidad de transporte de los buques metaneros en un solo viaje. Los buques metaneros son embarcaciones especiales construidas especialmente para el transporte de metano y gases inflamables.
Ahora veamos en detalle la cadena de suministro y tratamiento del gas natural.
Después de la extracción del producto, con la ayuda de metanoductos, el gas se transporta a instalaciones especiales que procederán a su licuefacción; las instalaciones pueden encontrarse cerca de las costas, normalmente en zonas portuarias, o en instalaciones off-shore, con estructuras flotantes ancladas al fondo marino.
Para llevar el gas al estado líquido, se inicia con un tratamiento de eliminación del dióxido de carbono y del sulfuro de hidrógeno, a continuación se realiza un preenfriamiento y se procede con la extracción de eventuales componentes pesados. En este punto, la temperatura del gas se reduce drásticamente a -163°C, por debajo de la temperatura de ebullición del metano, principal componente del gas natural.
Con tubos criogénicos, ubicados en muelles de carga, se inyecta gas natural licuado dentro de los tanques colocados en los buques metaneros. Estos barcos pueden transportar entre 150 y 200 mil metros cúbicos de metano, y existen dos tipos:
- El primer ejemplo es el de un barco con tanques integrados desarrollado por Gaztransport & Technigaz. Para esta tipología existen 2 versiones: la de Technigaz con depósitos constituidos por una barrera primaria elástica, formada por una membrana con nervaduras realizada con placas de acero; la disposición de las placas forma dos órdenes de nervaduras ortogonales entre sí y tienen la función de reducir las tensiones térmicas. La barrera secundaria está realizada con un material compuesto, el “tríplex”, consistente en una lámina de aluminio en un wafer de tejido de fibra de vidrio. El depósito se fija al casco interior con una espuma de poliuretano reforzada con fibras de vidrio. En cambio, la tipología desarrollada por Gaztransport prevé dos barreras compuestas por planchas planas soldadas (???), realizadas en una particular aleación metálica de acero y níquel, denominada “Invar”. Entre las dos barreras hay paneles aislantes y cámaras de aire, en las que se inyecta nitrógeno líquido para mantener la temperatura criogénica del gas natural. En este caso, el tanque se mantiene en el casco interno con cajas de aislamiento térmico de madera de balsa llenas de perlita.
- Otro ejemplo de buque metanero con tanques autoportante: la empresa Moss Rosenberg se enfrentó al problema de la resistencia a los esfuerzos inducidos por el peso del gas natural en los tanques, para solucionarlo diseñó buques metaneros con 4 o 6 tanques esféricos. Las bolas están aisladas con una capa de material aislante, entre ellas se pasa una cámara llena de nitrógeno para aumentar la capacidad de aislamiento y mantener baja la temperatura del tanque. Cada esfera está sostenida por una camisa cilíndrica que descansa sobre el casco del barco; este último está protegido de posibles fugas de gas con una barrera secundaria colocada en la base de las esferas.
El transportador de GNL transporta su carga de GNL a la planta de regasificación; tras haber sido fondeados y haber realizado la conexión a los brazos de descarga de las instalaciones portuarias, comienzan a trasvasar el GNL a los tanques de almacenamiento. Las plantas de regasificación pueden estar ubicadas en zonas portuarias, por lo que hablamos de una planta onshore en tierra firme, o de una plataforma, apoyada en el fondo del mar, que toma el nombre de offshore gravity based, o de floating storage and regasification unit, FSRU, un buque metanero, convertido para regasificación, anclado al fondo del mar, pero este tipo lo veremos más adelante.
Con las bombas a bordo del buque metanero, el GNL se descarga en los tanques de la planta, para una carga estándar se necesitan aproximadamente 12 horas. El GNL siempre se almacena en forma líquida, por lo que se adoptan tubos criogénicos especiales, que son capaces de gestionar y mantener la temperatura del gas licuado a -163 °C.
El GNL se almacena en tanques de doble coraza a presión atmosférica. La calota interior, en contacto con el GNL, está fabricada con aceros especiales con un 9% de níquel para evitar problemas de rotura por bajas temperaturas. La calota exterior, por otro lado, está hecha de hormigón pretensado. Entre el espacio intermedio de las dos carcasas hay un revestimiento aislante y otro revestimiento en la parte inferior de espuma de vidrio. Todos los tanques de GNL tienen forma cilíndrica y descansan sobre una base donde se encuentran aisladores sísmicos, para evitar roturas y pérdidas durante los choques de un sismo. Las fases de llenado y extracción del GNL se realizan en la parte superior, con la ayuda de una bomba sumergible; el techo está formado por una capa de aislamiento sostenida por cables de suspensión y un revestimiento de acero, revestido con un muro de hormigón armado. Los tanques pueden ser enterrados, para tener un menor impacto visual, pero tienen costos de construcción y mantenimiento muy altos, por lo que prefieren instalarse en la superficie, donde los costos son decididamente menores; la capacidad de un tanque puede variar entre 7.000 metros cúbicos y 160.000 metros cúbicos.
Una vez almacenado el GNL en los tanques, se puede proceder a la fase de regasificación, en plantas que vaporizan el gas licuado. Este tratamiento es muy delicado y se puede realizar con diferentes tecnologías, que se distinguen según la temperatura de operación, es decir, procesos a temperatura ambiente y superiores a la temperatura ambiente.
Para el proceso a temperatura ambiente se utiliza un vaporizador de agua de mar (open rack vaporizer). El funcionamiento es muy simple: dentro del vaporizador hay haces de tubos verticales, hechos de aleación de aluminio y recubiertos con una aleación de zinc para prevenir los fenómenos de corrosión inducidos por la sal marina, a través de los cuales fluye el GNL con un flujo que va de abajo hacia arriba; sobre estos tubos se hace caer agua de mar a temperatura ambiente, que transfiere su calor al haz de tubos permitiendo en su interior la vaporización del GNL. El agua de mar se recoge posteriormente para ser devuelta al mar a una temperatura de 4-5°C, prestando especial atención a la contención de sustancias nocivas para el medio ambiente. Se trata de una tecnología muy contrastada en la industria del GNL, utilizada principalmente en Europa, que al no utilizar una fuente de calor para calentar el GNL permite reducir las emisiones de CO2 a la atmósfera.
Esta tecnología también se utiliza en buques metaneros convertidos a FSRU, es decir, Floating Storage and Regasification Unit. Este buque en particular permite al mismo tiempo el transporte y regasificación de GNL una vez que llega a la zona de descarga cerca de la costa. Estos barcos son de una longitud que varía de 250 a 280 metros y de unos 40 metros de ancho, con una capacidad de aproximadamente 140.000 metros métricas y una producción anual de 2,5/3 millones de toneladas.
Para el proceso con temperatura superior a la ambiente se utiliza un vaporizador de llama sumergida (submerged combustion vaporizer), veamos juntos cómo funciona: para los sistemas de combustión sumergida encontramos un quemador colocado en un baño de agua, la cual constituye el fluido que calentará el GNL. Para la combustión del quemador se utiliza una pequeña cantidad de gas natural importado, generalmente un 1,5%, que es previamente precalentado. Los gases calientes producidos son conducidos a través de un sistema de distribución dentro del baño de agua caliente, el cual es atravesado por un haz de tubos que transporta el GNL que se vaporiza dentro del propio haz. El gas vaporizado se envía a la etapa de compresión y almacenamiento en tanques esféricos, para luego ser inyectado a la red de transporte y distribución.
Hemos llegado así al final de nuestro vídeo. Hemos visto todas las etapas de la cadena de suministro del gas natural licuado, desde la licuefacción en plantas costeras hasta su regasificación con tecnologías en constante evolución.
El GNL se almacena en tanques de doble coraza a presión atmosférica. La calota interior, en contacto con el GNL, está fabricada con aceros especiales con un 9% de níquel para evitar problemas de rotura por bajas temperaturas. La calota exterior, por otro lado, está hecha de hormigón pretensado. Entre el espacio intermedio de las dos carcasas hay un revestimiento aislante y otro revestimiento en la parte inferior de espuma de vidrio. Todos los tanques de GNL tienen forma cilíndrica y descansan sobre una base donde se encuentran aisladores sísmicos, para evitar roturas y pérdidas durante los choques de un sismo. Las fases de llenado y extracción del GNL se realizan en la parte superior, con la ayuda de una bomba sumergible; el techo está formado por una capa de aislamiento sostenida por cables de suspensión y un revestimiento de acero, revestido con un muro de hormigón armado. Los tanques pueden ser enterrados, para tener un menor impacto visual, pero tienen costos de construcción y mantenimiento muy altos, por lo que prefieren instalarse en la superficie, donde los costos son decididamente menores; la capacidad de un tanque puede variar entre 7.000 metros cúbicos y 160.000 metros cúbicos.
Una vez almacenado el GNL en los tanques, se puede proceder a la fase de regasificación, en plantas que vaporizan el gas licuado. Este tratamiento es muy delicado y se puede realizar con diferentes tecnologías, que se distinguen según la temperatura de operación, es decir, procesos a temperatura ambiente y superiores a la temperatura ambiente.
Para el proceso a temperatura ambiente se utiliza un vaporizador de agua de mar (open rack vaporizer). El funcionamiento es muy simple: dentro del vaporizador hay haces de tubos verticales, hechos de aleación de aluminio y recubiertos con una aleación de zinc para prevenir los fenómenos de corrosión inducidos por la sal marina, a través de los cuales fluye el GNL con un flujo que va de abajo hacia arriba; sobre estos tubos se hace caer agua de mar a temperatura ambiente, que transfiere su calor al haz de tubos permitiendo en su interior la vaporización del GNL. El agua de mar se recoge posteriormente para ser devuelta al mar a una temperatura de 4-5°C, prestando especial atención a la contención de sustancias nocivas para el medio ambiente. Se trata de una tecnología muy contrastada en la industria del GNL, utilizada principalmente en Europa, que al no utilizar una fuente de calor para calentar el GNL permite reducir las emisiones de CO2 a la atmósfera.
Esta tecnología también se utiliza en buques metaneros convertidos a FSRU, es decir, Floating Storage and Regasification Unit. Este buque en particular permite al mismo tiempo el transporte y regasificación de GNL una vez que llega a la zona de descarga cerca de la costa. Estos barcos son de una longitud que varía de 250 a 280 metros y de unos 40 metros de ancho, con una capacidad de aproximadamente 140.000 metros métricas y una producción anual de 2,5/3 millones de toneladas.
Para el proceso con temperatura superior a la ambiente se utiliza un vaporizador de llama sumergida (submerged combustion vaporizer), veamos juntos cómo funciona: para los sistemas de combustión sumergida encontramos un quemador colocado en un baño de agua, la cual constituye el fluido que calentará el GNL. Para la combustión del quemador se utiliza una pequeña cantidad de gas natural importado, generalmente un 1,5%, que es previamente precalentado. Los gases calientes producidos son conducidos a través de un sistema de distribución dentro del baño de agua caliente, el cual es atravesado por un haz de tubos que transporta el GNL que se vaporiza dentro del propio haz. El gas vaporizado se envía a la etapa de compresión y almacenamiento en tanques esféricos, para luego ser inyectado a la red de transporte y distribución.
Hemos llegado así al final de nuestro vídeo. Hemos visto todas las etapas de la cadena de suministro del gas natural licuado, desde la licuefacción en plantas costeras hasta su regasificación con tecnologías en constante evolución.