DÉCOUVRE NOTRE CANAL YOUTUBE
Comment un regazéifieur de gaz naturel liquide est-il transporté et comment fonctionne-t-il?
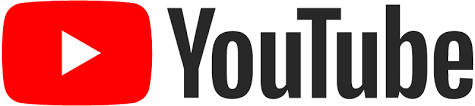
Comment un regazéifieur de gaz naturel liquide est-il transporté et comment fonctionne-t-il?
Dans notre précédente vidéo, nous avons parlé du gaz naturel et de ses caractéristiques, en examinant en détail toutes les étapes nécessaires à son extraction et les types de plantes.
Comme nous l’avons déjà mentionné, le gaz une fois extrait est raffiné et transporté par gazoducs ou méthanoducs jusqu’aux centrales électriques et aux habitations.
Mais comment le gaz extrait du gisement est-il transporté jusqu’à son utilisateur final ? Au mieux, il est transporté par voie terrestre à l’aide de pipelines, pour les territoires qui ont la chance d’être reliés aux pays fournisseurs, comme la plupart des pays européens avec la Russie. Pour les pays qui ne disposent pas de ces possibilités, ils doivent acheter le produit auprès de nations qui transportent le gaz naturel par voie maritime.
Le transport du gaz naturel par voie maritime est très délicat, nous parlons d’un produit composé à 98% de méthane, qui est hautement inflammable, et son transport dans de grandes citernes installées sur un navire peut être particulièrement risqué.
C’est pour cette raison que le gaz naturel doit être amené de son état aéroforme à un état liquide. Le gaz naturel liquide, également connu sous le nom de GNL (LNG en anglais), n’est pas aussi inflammable qu’à l’état aéré, et le volume du gaz est réduit de 600 fois, ce qui facilite et augmente la capacité de transport des méthaniers en un seul voyage. Les méthaniers sont des navires spéciaux construits spécifiquement pour transporter du méthane et des gaz inflammables.
Examinons maintenant en détail la chaîne de distribution et de traitement du gaz naturel.
Après l’extraction du produit, à l’aide de méthanoducs, le gaz est transporté vers des usines spéciales qui le liquéfieront ; les usines peuvent être situées près de la côte, généralement dans des zones portuaires, ou dans des usines off-shore, avec des structures flottantes ancrées au fond de la mer.
Pour amener le gaz à l’état liquide, nous commençons par un traitement visant à éliminer le dioxyde de carbone et le sulfure d’hydrogène, suivi d’un pré-refroidissement et de l’extraction de tout composant lourd. À ce point, la température du gaz est fortement abaissée à -163°C, en dessous de la température d’ébullition du méthane, le principal composant du gaz naturel.
À l’aide de tuyaux cryogéniques, situés sur les quais de chargement, le gaz naturel liquéfié est injecté dans les réservoirs des méthaniers. Ces navires particuliers peuvent transporter 150 à 200 000 mètres cubes de méthane, et il en existe deux types :
- Le premier exemple est le navire à réservoirs intégrés développé par Gaztransport & Technigaz. Il existe deux versions de ce type : celle de Technigaz avec des réservoirs constitués d’une barrière primaire élastique, formée par une membrane nervurée constituée de plaques d’acier ; la disposition des plaques forme deux rangées de nervures perpendiculaires l’une à l’autre et a pour fonction de réduire les contraintes thermiques. La barrière secondaire est constituée d’un matériau composite, le "triplex", composé d’une feuille d’aluminium dans une galette de tissu en fibre de verre. Le réservoir est fixé à la partie intérieure par une mousse de polyuréthane renforcée de fibres de verre. Le type mis au point par Gaztransport, en effet, comporte deux barrières constituées d’un placage plat soudé fait d’un alliage métallique spécial d’acier et de nickel, appelé invar. Entre les deux barrières se trouvent des panneaux isolants et des chambres à air, dans lesquelles de l’azote liquide est injecté pour maintenir la température du gaz cryogénique. Dans ce cas, le réservoir est maintenu à la coque intérieure par des caissons d’isolation thermique en bois de balsa rempli de perlite.
- Un autre exemple de méthanier avec des réservoirs autoportants : la société Moss Rosenberg a été confrontée au problème de la résistance aux contraintes induites par le poids du gaz naturel dans les réservoirs, et pour le résoudre, elle a conçu des méthaniers avec 4 ou 6 réservoirs sphériques. Les sphères sont isolées par une couche de matériau isolant, et une cavité remplie d’azote est passée entre elles pour augmenter la capacité d’isolation et maintenir la température du réservoir. Chaque sphère est soutenue par une enveloppe cylindrique qui repose sur la coque du navire ; Ce dernier est protégé contre les fuites de gaz par une barrière secondaire à la base des sphères.
Le méthanier transporte sa cargaison de GNL jusqu’à l’usine de regazéification ; après avoir été ancrés et reliés aux bras de déchargement des installations portuaires, ils commencent à transférer le GNL dans des réservoirs de stockage. Les usines de regazéification peuvent être situées dans des zones portuaires, nous parlons donc d’une usine onshore à terre, ou d’une plateforme, reposant sur le fond de la mer, que l’on appelle offshore gravity based, ou même d’une unité flottante de stockage et de regazéification, FSRU, un méthanier, converti pour la regazéification, ancré au fond de la mer, mais nous verrons cette typologie plus tard.
Comme nous l’avons déjà mentionné, le gaz une fois extrait est raffiné et transporté par gazoducs ou méthanoducs jusqu’aux centrales électriques et aux habitations.
Mais comment le gaz extrait du gisement est-il transporté jusqu’à son utilisateur final ? Au mieux, il est transporté par voie terrestre à l’aide de pipelines, pour les territoires qui ont la chance d’être reliés aux pays fournisseurs, comme la plupart des pays européens avec la Russie. Pour les pays qui ne disposent pas de ces possibilités, ils doivent acheter le produit auprès de nations qui transportent le gaz naturel par voie maritime.
Le transport du gaz naturel par voie maritime est très délicat, nous parlons d’un produit composé à 98% de méthane, qui est hautement inflammable, et son transport dans de grandes citernes installées sur un navire peut être particulièrement risqué.
C’est pour cette raison que le gaz naturel doit être amené de son état aéroforme à un état liquide. Le gaz naturel liquide, également connu sous le nom de GNL (LNG en anglais), n’est pas aussi inflammable qu’à l’état aéré, et le volume du gaz est réduit de 600 fois, ce qui facilite et augmente la capacité de transport des méthaniers en un seul voyage. Les méthaniers sont des navires spéciaux construits spécifiquement pour transporter du méthane et des gaz inflammables.
Examinons maintenant en détail la chaîne de distribution et de traitement du gaz naturel.
Après l’extraction du produit, à l’aide de méthanoducs, le gaz est transporté vers des usines spéciales qui le liquéfieront ; les usines peuvent être situées près de la côte, généralement dans des zones portuaires, ou dans des usines off-shore, avec des structures flottantes ancrées au fond de la mer.
Pour amener le gaz à l’état liquide, nous commençons par un traitement visant à éliminer le dioxyde de carbone et le sulfure d’hydrogène, suivi d’un pré-refroidissement et de l’extraction de tout composant lourd. À ce point, la température du gaz est fortement abaissée à -163°C, en dessous de la température d’ébullition du méthane, le principal composant du gaz naturel.
À l’aide de tuyaux cryogéniques, situés sur les quais de chargement, le gaz naturel liquéfié est injecté dans les réservoirs des méthaniers. Ces navires particuliers peuvent transporter 150 à 200 000 mètres cubes de méthane, et il en existe deux types :
- Le premier exemple est le navire à réservoirs intégrés développé par Gaztransport & Technigaz. Il existe deux versions de ce type : celle de Technigaz avec des réservoirs constitués d’une barrière primaire élastique, formée par une membrane nervurée constituée de plaques d’acier ; la disposition des plaques forme deux rangées de nervures perpendiculaires l’une à l’autre et a pour fonction de réduire les contraintes thermiques. La barrière secondaire est constituée d’un matériau composite, le "triplex", composé d’une feuille d’aluminium dans une galette de tissu en fibre de verre. Le réservoir est fixé à la partie intérieure par une mousse de polyuréthane renforcée de fibres de verre. Le type mis au point par Gaztransport, en effet, comporte deux barrières constituées d’un placage plat soudé fait d’un alliage métallique spécial d’acier et de nickel, appelé invar. Entre les deux barrières se trouvent des panneaux isolants et des chambres à air, dans lesquelles de l’azote liquide est injecté pour maintenir la température du gaz cryogénique. Dans ce cas, le réservoir est maintenu à la coque intérieure par des caissons d’isolation thermique en bois de balsa rempli de perlite.
- Un autre exemple de méthanier avec des réservoirs autoportants : la société Moss Rosenberg a été confrontée au problème de la résistance aux contraintes induites par le poids du gaz naturel dans les réservoirs, et pour le résoudre, elle a conçu des méthaniers avec 4 ou 6 réservoirs sphériques. Les sphères sont isolées par une couche de matériau isolant, et une cavité remplie d’azote est passée entre elles pour augmenter la capacité d’isolation et maintenir la température du réservoir. Chaque sphère est soutenue par une enveloppe cylindrique qui repose sur la coque du navire ; Ce dernier est protégé contre les fuites de gaz par une barrière secondaire à la base des sphères.
Le méthanier transporte sa cargaison de GNL jusqu’à l’usine de regazéification ; après avoir été ancrés et reliés aux bras de déchargement des installations portuaires, ils commencent à transférer le GNL dans des réservoirs de stockage. Les usines de regazéification peuvent être situées dans des zones portuaires, nous parlons donc d’une usine onshore à terre, ou d’une plateforme, reposant sur le fond de la mer, que l’on appelle offshore gravity based, ou même d’une unité flottante de stockage et de regazéification, FSRU, un méthanier, converti pour la regazéification, ancré au fond de la mer, mais nous verrons cette typologie plus tard.
Avec les pompes à bord du méthanier, le GNL est déchargé dans les réservoirs de l’usine ; un chargement standard prend environ 12 heures. Le GNL est toujours stocké sous forme liquide, c’est pourquoi on utilise des tuyaux cryogéniques spéciaux, capables de manipuler et de maintenir la température de -163°C du gaz liquéfié.
Le GNL est stocké dans des réservoirs à double coque à la pression atmosphérique. La coque intérieure, qui est en contact avec le GNL, est fabriquée en aciers spéciaux contenant 9 % de nickel pour éviter les problèmes de rupture dus aux basses températures. La coque extérieure, quant à elle, est constituée de béton précontraint. Entre la cavité des deux coquilles se trouve un revêtement isolant et un autre revêtement en mousse de verre sur le fond. Tous les réservoirs de GNL sont de forme cylindrique et reposent sur une base dotée d’isolateurs sismiques afin d’éviter les ruptures et les fuites lors des secousses d’un tremblement de terre. Le remplissage et l’extraction du GNL s’effectuent par le haut, à l’aide d’une pompe à immersion ; le plafond est constitué d’une couche d’isolation maintenue par des câbles de suspension et un revêtement en acier, recouvert d’un mur en béton armé. Les réservoirs peuvent être enterrés, pour avoir moins d’impact visuel, mais leurs coûts de construction et d’entretien sont très élevés, c’est pourquoi il est préférable de les installer en surface, où les coûts sont beaucoup plus réduits ; la capacité d’un réservoir peut varier entre 7 000 mètres cubes et 160 000 mètres cubes.
Une fois que le GNL est stocké dans des réservoirs, la phase de regazéification peut commencer, dans des usines qui vaporisent le gaz liquéfié. Ce traitement est très délicat et peut être réalisé à l’aide de différentes technologies, qui diffèrent en fonction de la température de fonctionnement, c’est-à-dire des processus à température ambiante et au-dessus.
Pour le processus à température ambiante, on utilise un vaporisateur (Open Rack). Le fonctionnement est très simple : à l’intérieur du vaporisateur se trouvent des faisceaux tubulaires verticaux, en alliage d’aluminium et recouverts d’un alliage de zinc pour éviter la corrosion induite par le sel marin, dans lesquels circule le GNL avec un débit qui va du bas vers le haut ; de l’eau de mer à température ambiante est aspergée sur ces tubes, qui transmet sa chaleur au faisceau tubulaire, permettant au GNL de se vaporiser à l’intérieur. L’eau de mer est ensuite recueillie pour être renvoyée à la mer à une température de 4-5 °C, en veillant particulièrement à ne pas contenir les substances nocives pour l’environnement. Il s’agit d’une technologie éprouvée dans l’industrie du GNL, principalement utilisée en Europe, qui n’utilise pas de source de chaleur pour chauffer le GNL et réduit ainsi les émissions de CO2 dans l’atmosphère.
Cette technologie est également utilisée sur les méthaniers convertis en FSRU, ou Floating Storage and Regasification Unit. Ce navire particulier permet le transport et la regazéification simultanés du GNL dès son arrivée dans la zone de déchargement près de la côte. Ces navires mesurent 250 à 280 mètres de long et environ 40 mètres de large, avec une capacité d’environ 140 000 mètres cubes et une production annuelle de 2,5 à 3 millions de tonnes.
Un vaporisateur à combustion submergée est utilisé pour le procédé à température supérieure, voyons comment il fonctionne : pour les systèmes à combustion submergée, on trouve un brûleur placé dans un bain d’eau, qui constitue le fluide qui va chauffer le GNL. Le brûleur utilise une petite quantité de gaz naturel importé, généralement 1,5 %, pour la combustion, qui est préalablement préchauffée. Le gaz chaud produit est acheminé par un système de distribution dans le bain d’eau chaude, qui est traversé par un faisceau de tubes qui transporte le GNL qui se vaporise dans le faisceau. Le gaz vaporisé est envoyé pour être comprimé et stocké dans des réservoirs sphériques, puis alimente le réseau de transport et de distribution.
Pour le procédé à température supérieure, on utilise un vaporisateur à combustion submergée, voyons comment il fonctionne : pour les systèmes à combustion submergée, on trouve un brûleur placé dans un bain d’eau, qui constitue le fluide qui va chauffer le GNL. Le brûleur utilise une petite quantité de gaz naturel importé, généralement 1,5 %, pour la combustion, qui est préalablement préchauffée. Le gaz chaud produit est acheminé par un système de distribution dans le bain d’eau chaude, qui est traversé par un faisceau de tubes qui transporte le GNL qui se vaporise dans le faisceau. Le gaz vaporisé est envoyé pour être comprimé et stocké dans des réservoirs sphériques, puis alimente le réseau de transport et de distribution.
Ceci nous amène à la fin de notre vidéo. Nous avons vu toutes les étapes de la chaîne des liquides de gaz naturel, de la liquéfaction dans les usines côtières à sa regazéification avec des technologies en constante évolution.
Le GNL est stocké dans des réservoirs à double coque à la pression atmosphérique. La coque intérieure, qui est en contact avec le GNL, est fabriquée en aciers spéciaux contenant 9 % de nickel pour éviter les problèmes de rupture dus aux basses températures. La coque extérieure, quant à elle, est constituée de béton précontraint. Entre la cavité des deux coquilles se trouve un revêtement isolant et un autre revêtement en mousse de verre sur le fond. Tous les réservoirs de GNL sont de forme cylindrique et reposent sur une base dotée d’isolateurs sismiques afin d’éviter les ruptures et les fuites lors des secousses d’un tremblement de terre. Le remplissage et l’extraction du GNL s’effectuent par le haut, à l’aide d’une pompe à immersion ; le plafond est constitué d’une couche d’isolation maintenue par des câbles de suspension et un revêtement en acier, recouvert d’un mur en béton armé. Les réservoirs peuvent être enterrés, pour avoir moins d’impact visuel, mais leurs coûts de construction et d’entretien sont très élevés, c’est pourquoi il est préférable de les installer en surface, où les coûts sont beaucoup plus réduits ; la capacité d’un réservoir peut varier entre 7 000 mètres cubes et 160 000 mètres cubes.
Une fois que le GNL est stocké dans des réservoirs, la phase de regazéification peut commencer, dans des usines qui vaporisent le gaz liquéfié. Ce traitement est très délicat et peut être réalisé à l’aide de différentes technologies, qui diffèrent en fonction de la température de fonctionnement, c’est-à-dire des processus à température ambiante et au-dessus.
Pour le processus à température ambiante, on utilise un vaporisateur (Open Rack). Le fonctionnement est très simple : à l’intérieur du vaporisateur se trouvent des faisceaux tubulaires verticaux, en alliage d’aluminium et recouverts d’un alliage de zinc pour éviter la corrosion induite par le sel marin, dans lesquels circule le GNL avec un débit qui va du bas vers le haut ; de l’eau de mer à température ambiante est aspergée sur ces tubes, qui transmet sa chaleur au faisceau tubulaire, permettant au GNL de se vaporiser à l’intérieur. L’eau de mer est ensuite recueillie pour être renvoyée à la mer à une température de 4-5 °C, en veillant particulièrement à ne pas contenir les substances nocives pour l’environnement. Il s’agit d’une technologie éprouvée dans l’industrie du GNL, principalement utilisée en Europe, qui n’utilise pas de source de chaleur pour chauffer le GNL et réduit ainsi les émissions de CO2 dans l’atmosphère.
Cette technologie est également utilisée sur les méthaniers convertis en FSRU, ou Floating Storage and Regasification Unit. Ce navire particulier permet le transport et la regazéification simultanés du GNL dès son arrivée dans la zone de déchargement près de la côte. Ces navires mesurent 250 à 280 mètres de long et environ 40 mètres de large, avec une capacité d’environ 140 000 mètres cubes et une production annuelle de 2,5 à 3 millions de tonnes.
Un vaporisateur à combustion submergée est utilisé pour le procédé à température supérieure, voyons comment il fonctionne : pour les systèmes à combustion submergée, on trouve un brûleur placé dans un bain d’eau, qui constitue le fluide qui va chauffer le GNL. Le brûleur utilise une petite quantité de gaz naturel importé, généralement 1,5 %, pour la combustion, qui est préalablement préchauffée. Le gaz chaud produit est acheminé par un système de distribution dans le bain d’eau chaude, qui est traversé par un faisceau de tubes qui transporte le GNL qui se vaporise dans le faisceau. Le gaz vaporisé est envoyé pour être comprimé et stocké dans des réservoirs sphériques, puis alimente le réseau de transport et de distribution.
Pour le procédé à température supérieure, on utilise un vaporisateur à combustion submergée, voyons comment il fonctionne : pour les systèmes à combustion submergée, on trouve un brûleur placé dans un bain d’eau, qui constitue le fluide qui va chauffer le GNL. Le brûleur utilise une petite quantité de gaz naturel importé, généralement 1,5 %, pour la combustion, qui est préalablement préchauffée. Le gaz chaud produit est acheminé par un système de distribution dans le bain d’eau chaude, qui est traversé par un faisceau de tubes qui transporte le GNL qui se vaporise dans le faisceau. Le gaz vaporisé est envoyé pour être comprimé et stocké dans des réservoirs sphériques, puis alimente le réseau de transport et de distribution.
Ceci nous amène à la fin de notre vidéo. Nous avons vu toutes les étapes de la chaîne des liquides de gaz naturel, de la liquéfaction dans les usines côtières à sa regazéification avec des technologies en constante évolution.